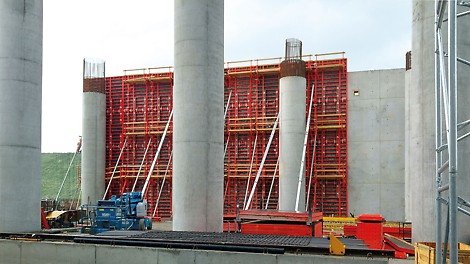

Download Press Release
The images in more detail
Opened in 2018, the airport is located north-west of Istanbul and features six runways and, in ten years time, is expected to handle a larger passenger volume than does currently the world´s largest airport in Atlanta. PERI systems were not only used in the realisation of the main terminal building but also deployed for constructing various other facilities. A range of PERI systems were used to construct, for example, a muliti-storey car park, maintenance building, fire station, cargo building, energy building, wastewater treatment plant, subway terminal, passenger and luggage tunnels, security building and a mosque. A total of 13 different building contractors participated in the construction of the airport using PERI systems.
Walls and columns in architectural concrete quality with TRIO
Using state-of-the-art PERI formwork technology, the construction team successfully formed the high walls and columns in the best architectural concrete quality. In one part of the building, walls and slabs up to 14 m high with a thickness of up to 1.75 m were realised. In the process, the slab beams featured heights of up to 2.30 m. Because of the system´s numerous advantages, the construction team formed the reinforced concrete core walls with TRIO wall formwork. One particular advantage of using TRIO is, among other things, the possibility of moving large-sized units by crane. This also saved valuable working time during the Istanbul Airport project. The minimum of different components and the universally applicable BFD Alignment Coupler likewise accelerated and simplified forming operations with the proven panel formwork.
High level of productivity through movable working platforms
For processing the approx. 220,000 m² slab area at a height of 17.50 m, the construction teams installed a total of 15,500 m² of platforms with spans of up to 15 m and supported by PERI UP Flex shoring. In order to fulfil all the requirements of the clients, the PERI UP scaffolding completely shielded site activities from ongoing airport operations. The scaffolding construction simultaneously served as working scaffold. Installation of system decking provided protection for the area under the platforms so that the check-in desks could be installed beforehand. Due to the tight schedule and the enormous slab area, it was also necessary to minimise both the assembly and moving times for the working platforms. As a result, PERI used transportation wheels in order to easily move the platform elements by hand in a longitudinal direction. Thanks to the high degree of system rigidity, an area of up to 540 m² could be moved as one unit. Independent of the height of the platforms - some of the working platforms were mounted at heights of up to 40 m - the LGS elements could be manually moved to their next place of use in only 15 minutes.
Time savings during construction operations
Last but not least, PERI worked closely together with all participants to ensure that the large quantities of materials were delivered on a just-in-time basis in spite of the short lead time. Right from the very beginning, PERI engineers and supervisors provided extremely reliable support through comprehensive on-site assistance in order to ensure that all system devices were efficiently used from the outset. Thanks to the close cooperation between PERI Turkey and PERI GmbH along with the help of the state-of-the-art system solutions, it was possible to successfully realise this extremely important project and in the shortest possible time.