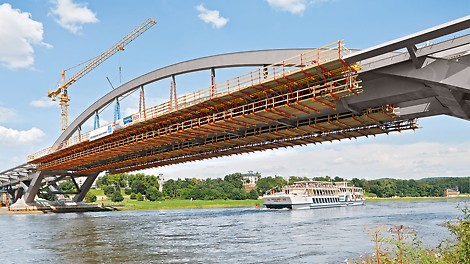
Trust PERI for new or refurbished bridge projects
Not only are a significant number of new bridge structures being built of all types and sizes, but critically many existing bridge assets require maintenance and repair to meet the demands of society.
We can offer integrated products and systems, which produce efficient and clever solutions when combined together. PERI UP scaffolding can provide access and working platforms, and combined with our civil engineering range VARIOKIT, can be suspended or configured for any geometry required.
Either for new structures or the refurbishment and reinforcement of existing ones, we have an extensive range of formwork systems including lightweight handset to bespoke heavy-duty steel forms. Finally, our shoring systems, based on a modular lightweight concept of minimum pieces with maximum capacity, provide the reassurrance required during the construction phase to support the structure until it is capable of supporting its own mass.
At the leading edge of infrastructure technology
PERI's self-climbing formwork, tunnel carriages and bridge systems are sophisticated temporary works systems designed to be wholly dependable, reliable and provide the most efficient and safe construction progress. Independent formwork moving and climbing operations are possible regardless of whether the structure is aligned horizontally, vertically, inclined or curved.
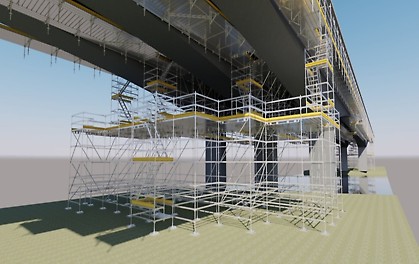
This system technology is integrated into the unique pool of knowledge and experience of PERI Engineering. Over 1,300 projects and application engineers advise, develop and coordinate formwork and scaffolding solutions for customers worldwide - always in close cooperation with multitude of stakeholders associated with bridge projects.
Structures, cross sections and project examples
The components of a bridge are divided into substructure, superstructure and equipment. Which of the structures and superstructure cross-sections are used, depends on factors such as length, span, materials, type of use, loads and the topographical and geological conditions.
They are classified according to different aspects; potentially by their positioning in a geographical feature like river, valley or slope and according to their construction material in concrete, steel, wood or composite.
When considering the structural design, the focus is on the structural/superstructure cross-sections and the component groups.
The supporting structures are generally differentiated according to:
- Beam bridges
- Arched bridges
- Suspension / cable-stayed bridges
The cross sections of the superstructure are divided into:
- Solid plate / girder
- Plate beam
- Hollow box
- Trough
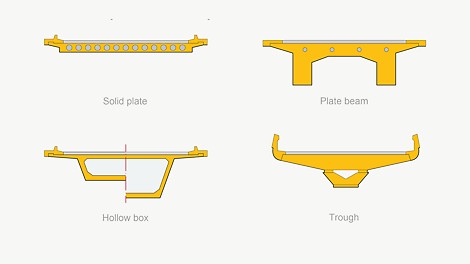
PERI solutions for bridge superstructures and project examples
In general, bridges are divided according to their construction principle into in-situ concrete bridges, prefabricated and segmental bridges. There are four different construction methods for in-situ concrete bridges:
- building with conventional formwork and shoring
- building with advancing shoring / moveable scaffold
- building using the incremental launching method
- building with cantilever construction
Conventional formwork
This method is suitable for bridge structures with a low overall height and free access to the underside of the bridge. Depending on the level of the terrain, the shoring can be set up as stationary or movable. The loads from the structural formwork are transferred to the subsoil via the shoring/falsework.
Advancing / Movable Scaffold
This process is suitable for bridge structures with large pier heights and the underside of the bridge that is difficult to access. The feed gantry is one of the self-supporting formwork and scaffolding systems. After concreting in sections, the system is moved in the longitudinal axis with movable support beams - without any additional support between the bridge piers. The loads from the structural formwork are absorbed by the feed gantry and passed on to the piers of the bridge.
Incremental launching
With this process a high level of cost-effectiveness is possible thanks to uniform work processes. The superstructure will be constructed whilst stationary in sections in a field factory behind the bridge. After a new bridge section has been manufactured, it is lifted hydraulically and moved in the direction of the longitudinal axis until the stem rests securely on the support saddle of the next support.
Cantilever
The cantilever construction method is suitable for bridge structures with large spans and difficult topography - for example when crossing bodies of water, valley cuts, etc. With cantilever construction, the superstructure is constructed symmetrically from the pillars according to the balance beam. There is therefore a front carriage on both sides of the pillar, which moves the formwork to the next concreting section via a cantilever arm structure. There the next construction phase is added to both freely cantilevered component ends.
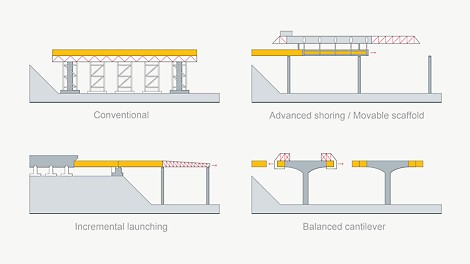
VARIOKIT and custom steel formwork provide the ultimate bridge system
Our versatile engineering kit can be configured for use in a wide range of applications, and complimented with bespoke steel forms as required.Our bridge solutions are generally based on a single system, the VARIOKIT engineering construction kit, which can purchased or rented on a project-specific basis. VARIOKIT can create a wide variety of supporting structures, for example trusses or shoring towers. At the same time, the engineering construction kit is also the basis for all types of formwork processes - from the cornice cap console, cantilever construction, steel composite carriages to climbing formwork. With electric and hydraulic components, the VARIOKIT engineering kit can be expanded to include mechanical functions that enable the formwork elements to be raised, lowered, moved, climbed, shuttered and stripped.
With only three core components - the steel bar SRU, the climbing rail RCS, the heavy-duty spindle SLS, approximately 80% of all heavy-duty structures can be constructed with these three core component parts. Another 15% are also system components from the VARIOKIT engineering kit; the remaining 5% are project-specific special components. This consistently simplified construction principle of the VARIOKIT engineering construction kit enables a high level of safety and speed - both during assembly and dismantling, but also in use on the construction site.
Another key system advantage of VARIOKIT is its ability to be combined with the PERI UP scaffolding, protection and shoring system. Both systems are based on the metric scale with a grid of 12.5, 25 and 50 cm and are therefore completely compatible with each other.